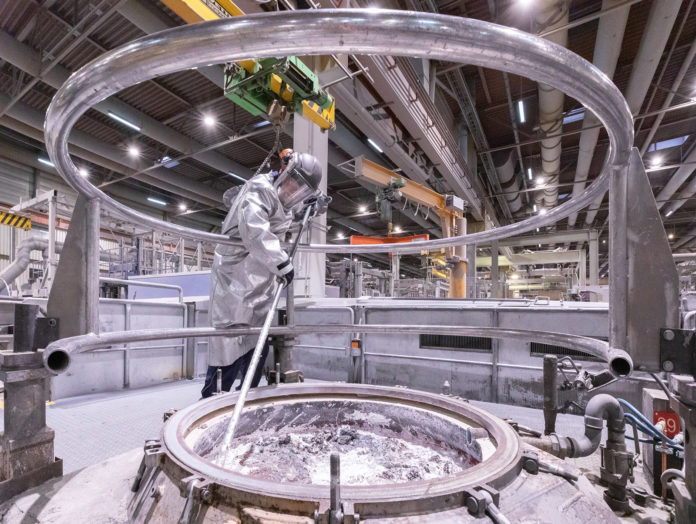
The BMW Group’s light metal foundry in Landshut has once again been certified by an independent party for its sustainable use of aluminium – meeting the standards of the Aluminium Stewardship Initiative (ASI), an international non-profit organisation supported by environmental and industrial associations, aluminium producers and processing companies. The ASI defines sustainability criteria for an environmentally and socially responsible aluminium value chain.
“Sustainable extraction of raw materials and conscious use of resources play a key role for our in-house component production and our global supplier network,” says Dr Joachim Post, member of the Board of Management of BMW AG responsible for Purchasing and Supplier Network.
“Sourcing aluminium produced using solar power for our in-house component production lowers our CO2 emissions significantly. The circular economy is also key to reducing emissions and conserving natural resources. Going forward, the aim is to build our new vehicles with 50 percent secondary raw materials.”
Solar aluminium meets more than a third of annual requirements
Landshut’s light metal foundry, the BMW Group’s only production facility for light metal casting in Europe, is among the most advanced, most sustainable foundries in the world. Thanks to its use of inorganic sand cores, the casting process is virtually emission-free. The light metal foundry began sourcing aluminium produced using solar power in 2021.
Since producing aluminium is highly energy-intensive, the use of green power such as solar electricity offers considerable potential for reducing CO2 emissions. The tens of thousands of tonnes of solar aluminium supplied in this way meet more than a third of annual requirements for the light metal foundry at Plant Landshut.
CO2-optimised recycling loop with closed foundry loop
Along with steel, aluminium accounts for the largest share, by weight, of the materials used in BMW Group vehicles. Around two thirds of the aluminium used in Landshut comes from a recycling loop – with almost two thirds of this from the foundry’s own closed loop. In this way, the BMW Group is consciously reducing its use of more CO2-intensive primary aluminium in favour of a CO2-optimised recycling loop. Green power is also used to produce it.
The BMW Group has a long tradition of responsible use of aluminium. For more than ten years, the light metal foundry has been working with local processors to implement a recycling loop for post-production scrap metal salvaged from the foundry process. The decisive factor here is clean separation of aluminium residues. Residues are collected from all casting and mechanical processing stations according to type, so materials with different compositions are not mixed. This means that, after reconditioning, aluminium waste can be reused to manufacture the same components.
“The BMW Group has supported the Aluminium Stewardship Initiative from the beginning,” says Dr Stefan Kasperowski, head of BMW Group Plant Landshut and the light metal foundry, which is the largest production area at the plant in Lower Bavaria. “We are fully aware of our responsibility and value sustainable production of raw materials for our manufacturing.”
Last year, employees at the light metal foundry produced around 3.3 million cast components with a total weight of more than 73,000 tonnes. The scope of production includes engine components such as cylinder heads and crankcases, components for electric drive trains and large-scale structural components for vehicle bodies.
The responsibility of the BMW Group extends beyond recycling to the aluminium used. The conditions under which the raw material bauxite is extracted by open cast mining and processed in countries like Australia, Brazil and Guinea are also important to the company.
The BMW Group is in direct contact with aluminium suppliers and recycling partners in an effort to gradually expand ASI certification to the entire material cycle – starting with the producing mines.
The light metal foundry has now been certified to the ASI Performance Standard for the second time. The auditing criteria require evidence of material stewardship, such as a holistic lifecycle analysis for the company’s own products and a comprehensive recycling strategy, as well as compliance with standards for transparency, overall management and corporate integrity. The initial successful certification in accordance with the criterion of material stewardship took place in December 2019.